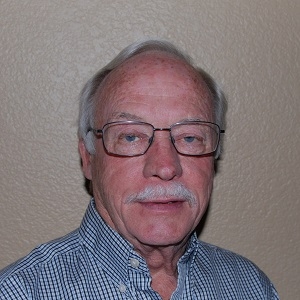
Competing with AI in the Workforce is the 2nd installment of Ron Wilson’s blog posts on how our technological advances directly impact our day-to-day.
Careers Most Likely to be Impacted by AI
Another question I asked AI was to identify 10 careers most likely to be replaced or heavily disrupted by AI in the coming years. As can be seen these roles especially reliant on involve repetitive, rule-based, or digital tasks:
Data Entry Clerks
- Why at risk: Repetitive and structured tasks are ideal for automation.
- AI alternative: OCR (optical character recognition) + machine learning systems can process massive volumes of data instantly.
Telemarketers
- Why at risk: Scripted phone calls and customer engagement can be mimicked by AI voice agents.
- AI alternative: AI-powered call bots with natural language processing.
I have been on calls as shown in the TikTok video. Having been on calls like I am curious if it was person or AI I was visiting with?
Retail Cashiers
- Why at risk: Self-checkout systems and AI-powered kiosks are increasingly common.
- AI alternative: Computer vision + payment automation.
We are seeing retailers needing to modify the self-checkout process and provide a personal touch to handle issues that arise during check out. The customer skills needed by the employee is empathy for the frustration the customer is experiencing and potential theft vs an error in the scanning process.
Fast Food Workers (Certain Roles)
- Why at risk: Order-taking, basic food assembly, and payment are being automated.
- AI alternative: Kiosks + kitchen robots (e.g., Flippy the burger-flipping robot).
Proofreaders and Copy Editors (Basic Editing)
- Why at risk: AI grammar checkers (e.g., Grammarly, ChatGPT) handle grammar and style with high accuracy.
- AI alternative: Language models trained on style, tone, and grammar rules.
Important roles are needed to address industry and generational language models.
Basic Legal Assistants / Paralegals
- Why at risk: Document review, legal research, and contract analysis can be automated.
- AI alternative: Legal AI platforms like Harvey AI, Casetext, or DoNotPay.
Routine Accounting / Bookkeeping
- Why at risk: Data entry, reconciliations, and reports can be handled by AI-integrated platforms.
- AI alternative: AI within QuickBooks, Xero, and other accounting tools.
Basic Customer Support Representatives
- Why at risk: Tier 1 support (FAQ-type questions) is now handled by chatbots and voice agents.
- AI alternative: AI-powered customer service platforms like Zendesk AI or Intercom.
Transport Dispatchers / Schedulers
- Why at risk: AI can optimize logistics, routes, and schedules in real-time better than humans.
- AI alternative: AI logistics platforms with real-time optimization algorithms.
Market Research Analysts (Entry-Level)
- Why at risk: AI can scan and synthesize market data, trends, and customer sentiment faster than humans.
- AI alternative: Tools like ChatGPT for research summaries, or platforms like Crayon and Similarweb.
Important Note:
AI may replace tasks, not necessarily entire jobs. Many roles will evolve, not disappear — humans who can manage AI, interpret results, and make strategic decisions will remain highly valuable.
Careers Least Likely to be Replaced by AI
10 careers least likely to be replaced by AI — these rely heavily on human judgment, emotional intelligence, creativity, or physical presence:
Mental Health Professionals (Therapists, Counselors, Social Workers)
- Why safe: Deep empathy, trust-building, and emotional nuance are difficult for AI to replicate.
- Human edge: Relationship, listening, and emotional discernment.
AI support to the Mental Health Professionals:
- Analyze patient mood/sentiment from voice/text patterns
- Track therapy progress with AI-generated session summaries
- Suggest evidence-based interventions based on client data
Example: An AI assistant could flag signs of depression based on journaling apps between therapy sessions.
Teachers and Educators
- Why safe: Teaching is about more than knowledge delivery — it’s mentoring, adapting to student needs, and fostering growth.
- Human edge: Engagement, encouragement, and personalization.
AI will support Teachers and Educators:
- Customize lesson plans based on student performance
- Automate grading and feedback on assignments
- Offer tutoring/chatbots for homework help outside class
Example: A teacher uses AI to detect learning gaps and adjust curriculum per student.
Skilled Trades (Electricians, Plumbers, Carpenters)
- Why safe: On-site problem-solving and physical dexterity are hard to automate.
- Human edge: Precision, adaptability, and hands-on troubleshooting.
AI will support Skilled Trades:
- AR/AI-powered glasses to overlay repair instructions in real time
- Predictive maintenance alerts for clients via smart systems
- Digital twins to simulate repairs before doing physical work
Example: A plumber uses AI to analyze smart sensor data from a home water system and spot hidden leaks. Remote diagnostics to determine severity of the event and skill level and resources needed to complete the repair, including ordering of parts.
Healthcare Providers (Doctors, Nurses, Surgeons)
- Why safe: AI can assist with diagnostics, but humans are needed for procedures, patient care, and ethical decision-making.
- Human edge: Touch, care, and accountability in life-or-death decisions.
AI will support Healthcare Providers:
- Diagnoses faster with image recognition (e.g., radiology, dermatology)
- Analyze patient history to recommend treatments
- Predict health risks with AI-powered analytics
Example: A doctor uses AI to scan 10,000 patient records and identify early signs of diabetes trends.
Creative Professionals (Artists, Designers, Writers)
- Why safe-ish: While AI can generate content, original vision, storytelling, and emotional connection remain uniquely human.
- Human edge: Innovation, taste, and authentic voice.
AI will support Creative Professionals:
- Generate rough drafts or design ideas to spark creativity
- Suggest improvements based on audience data or engagement
- Automate routine tasks (resizing images, SEO tagging)
Example: A designer uses AI to create 10 mockup variations, then customizes the best one.
Leadership Roles (Executives, Managers, Strategic Planners)
- Why safe: AI can inform decisions, but leadership involves vision, inspiration, and accountability.
- Human edge: Motivation, decision-making under uncertainty, and moral judgment.
AI will support Leadership Roles:
- Analyze internal data to guide strategic decisions
- Identify trends and risks before they emerge
- Support communication with AI-written summaries or talking points
Example: A CEO uses AI to scan market shifts and adjust business strategy in real time.
Clergy and Spiritual Leaders
- Why safe: AI can reference scripture, but it can’t provide spiritual presence, guidance, or personal discernment.
- Human edge: Compassion, faith leadership, and community building.
AI will support Clergy and Spiritual Leaders:
- Organize sermon content and find relevant scripture instantly
- Help manage community events and communication
- Offer AI prayer or meditation prompts for congregants
Example: A pastor uses AI to pull biblical context, commentary, and sermon illustrations in minutes.
Emergency Responders (Firefighters, Police, Paramedics)
- Why safe: Urgency, unpredictability, and hands-on rescue require real people.
- Human edge: Courage, judgment under pressure, physical intervention. Emergency Responders
AI will support Emergency Responders:
- AI-powered drones and robots to assess hazardous environments
- Real-time GPS and dispatch optimization
- Predictive analytics for crisis hotspots (e.g., fire risks, overdoses)
Example: A firefighter uses AI drone footage to locate trapped civilians before entering a building.
Childcare and Eldercare Workers
- Why safe: Caring for the vulnerable requires human touch, empathy, and real-time responsiveness.
- Human edge: Trust, comfort, and personal interaction.
AI will support Childcare and Eldercare Workers:
- Smart monitoring for safety alerts (falls, irregular activity)
- AI reminders for medication and schedule coordination
- Learning tools personalized for child development stages
Example: A caregiver gets an AI alert that an elderly client hasn’t eaten in 10 hours.
Human Resources and Organizational Development
- Why safe: Hiring, conflict resolution, and culture-building require deep human insight.
- Human edge: Interpersonal dynamics, negotiation, and values alignment.
AI will support Human Resources and Organizational Development by:
- Screen resumes for qualifications and cultural fit
- Identify burnout or turnover risk via employee behavior data
- Facilitate DEI goals by tracking equity in promotions and pay
Example: HR uses AI to generate personalized development plans for each employee.
Final Insight:
Careers that blend emotional intelligence, physical presence, creativity, and ethical judgment are the most AI-resistant. The future of work isn’t about beating machines — it’s about being more human than ever.
AI is a superpower for these roles — not a replacement. The best outcomes happen when humans do what machines can’t, and machines do what humans shouldn’t have to.
Preparing to apply and utilize AI in your current role — and planning your career path with AI in mind — means developing the right mindset, skills, and strategic habits.